You know what it takes to carry your project plans forward. Some of you have been delivering projects for years. Every so often it helps to brush up on all the little things that help make your project planning skills optimized for the projects you’re working on today.
Follow our 20 tips that serve as good reminders for helping you execute your projects on time and under budget. Where helpful, we’ve added links to some of the ProjectManager.com tutorials, articles and even support videos, too. Even though you might not be a user of our particular software, these tutorials offer detailed views and step-by-step walkthroughs of how to apply some of these tips in action.
1. Link Plans To Timesheets
Your project plan should be linked to your project team’s timesheet app. This means that as they work on tasks and make progress towards completing them, the schedule will automatically update to say that the work is underway. It’s a fast way of getting status updates where no one has to do any extra work.
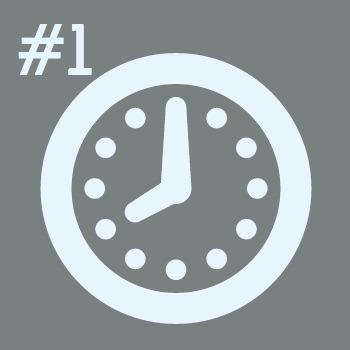
2. Add New Tasks Regularly
It’s no small task remembering to add every task, especially when you’ve got back-to-back meetings, phone calls, fires to put out and constraints like the 8-5 work week. Try to add new tasks as you go, when you’re on the go, rather than at the end of the week. Use your mobile phone to quickly jot down tasks when you’re chatting with that colleague or when you’ve figured out how to put out that fire. When you sit back at your desk, add your captured notes right away. Consider task tracking part of your daily multi-tasking effort.
3. Create Baselines
Take a baseline of your plan. This is a snapshot in time. It’s useful because you can then look back and see what was originally agreed and how things have changed since then. Check out Jennifer Bridges video training guide on
how to create baselines.
4. Add Resources
Each task on your plan should be assigned to a person, rather than floating in the breeze with no accountability. That not only helps you understand who is doing what, it helps them see their complete work program and plan their time accordingly.
5. Use Milestones
Milestones mark key points in the project like the completion of a phase or the start of a new tranche of work. They are also really helpful when it comes to reporting, as you can measure your progress against these key points and not every single task.
6. Establish The Critical Path
The critical path is the shortest path through the project. If anything along this route changes, such as more work being added, then the project will take longer. If you know the tasks on the critical path, you can make sure that they don’t slow down so you will reach your end date as planned. To learn more about how to determine your project’s critical path,
check out this video tutorial with Jennifer Bridges.
7. Involve Your Team
You can’t produce a plan by yourself. Make sure that your whole project team gets involved—and stays involved. They will have useful insight into the work that needs to be done.
8. Get It Approved
Once your plan is produced ask to discuss it with your sponsor. Get them to approve the plan as it stands so that you have a clear mandate to proceed.
9. Use Change Control
When the plan changes (and it will!) use a formal change control process to evaluate the change and then update the plan. You might want to take another baseline view at this point. Change control helps you manage changes in a structured way.
10. Be Iterative
Don’t expect to get it right first time. An iterative plan is one that evolves over time as more clarity is gained on the project. This is the way that Agile project teams work, and it’s also something you can do in a non-Agile environment.
11. Do Risky Work First
Put the tasks with the highest degree of risk at the beginning of the project, if you can. Then if anything goes wrong you have the longest possible time to sort it out!
12: Establish Costs
How much are your tasks going to cost? Make sure you prepare budget estimates for each task as this is a great way to get a comprehensive project budget.
13. Use Online Tools
Online project management tools are the easiest way to manage your project plans. Anyone can make changes from wherever they are, or if you prefer you can limit access to only yourself. Being online makes it easier to check status or to add a new task even if you aren’t at your desk. Read Jason Westland’s article on how to get the most out of your online tools
here.
14. Use a Gantt Chart
Gantt charts are an easy way to visualize the project and the work involved. You can also see how tasks link together and how long the whole thing is going to take.
15. Create Dependencies
Dependencies are the way in which tasks link to each other. Sometimes one task has to finish before another one can start. Or a task has to start at the same time as another task. It’s easy to add dependencies on a Gantt chart or a project schedule, and your software will automate the planning to show you how long the work will take once all the dependencies are taken into account.
16. Let Your Team Update It
If you are the only person who can update the plan, then more of the work falls to you. Find ways to let your trusted project team members update certain tasks so that you split the burden between you. This could be automatically through an interface (like timesheets) or directly into the plan itself.
17. Plan Backwards
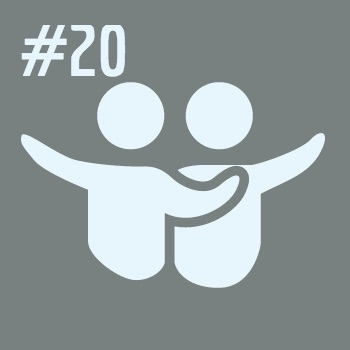
You might not be able to do this on all projects, but if you have a fixed date in mind for the delivery of your work then planning back from that will help you work out if you have enough time to do everything. If you find out that you don’t have enough time, you can then work out how to handle that!
18. Control Scope Creep
Scope creep is where extra work is added to the plan in an uncontrolled way. Make sure that everyone on the team knows that all changes have to go through the formal process so that you don’t find yourself working on a never ending project.
19. Add Contingency Time
Projects always take longer than you expect because generally you are doing something that the company has not done before ,which makes it hard to plan accurately. Add some contingency time of between 5% and 20% to allow for this and for unforeseen problems.
20. Share It
Make sure your plan is accessible to everyone on the team by sharing it. Someone will spot something that isn’t accurate, and together you will be able to work on it and get a better quality plan as a result.
Plan online with your whole project team using ProjectManager.com. It’s fast, easy to use and requires no training. Everyone will be looking at professional Gantt charts and sleek reports within minutes.